Additive Manufacturing|Topology Design of Thermal-Mechanical Coupling Structure Based on Multi-objective Optimization
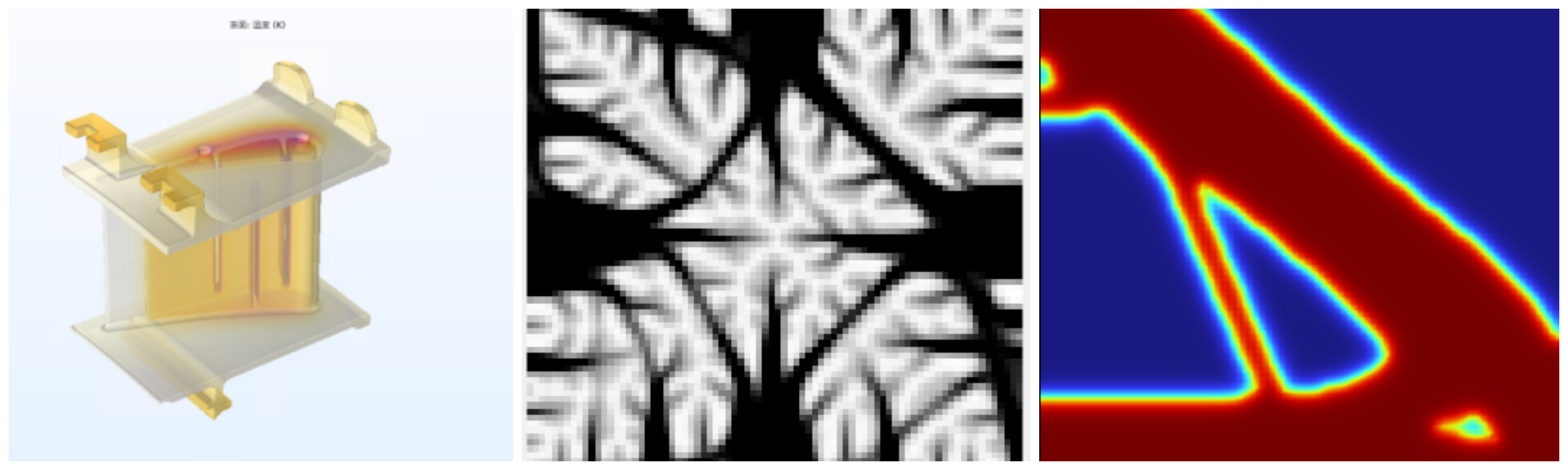
Out of interest, I joined my manufacturing course teacher Kun Li’s laboratory (HπAM of State Key Laboratory of Mechanical Transmission in Chongqing University) to learn about engineering analysis of additive manufacturing, mainly focusing on shape memory alloys and multi-objective based Optimal Thermal-Mechanical Coupling Structure Topology Design
The research projects displayed on this website are currently in a confidential state. Due to the special nature of the projects, it is inconvenient for me to display most of the contents publicly. Please understand and cooperate. For more information, welcome to contact me for further discussion and detailed introduction.
本网站展示的研究项目目前处于保密状态,鉴于项目的特殊性质,我对大部分内容不方便进行公开展示。请谅解并予以配合。如需了解更多信息,欢迎与我联系以获得进一步讨论和详细介绍。
I hope to design specially optimized 3D printed Ni-Ti shape memory alloy actuators with high explosive force, applied to the micro-robot joints.
In order to achieve such a goal, I asked doctoral students about the design process and learned Comsol, which I didn’t know before. At the same time, self-study the basic courses of mechanics, heat and materials.
Since the project is still in progress and there is a special nature of confidentiality, I am not allowed to show the details of the research privately. I will only show some screenshots of my early learning process below
Comsol natural convection simulation
Comsol heat transfer simulation
Comsol thermal coupling simulation (thermal stress analysis)
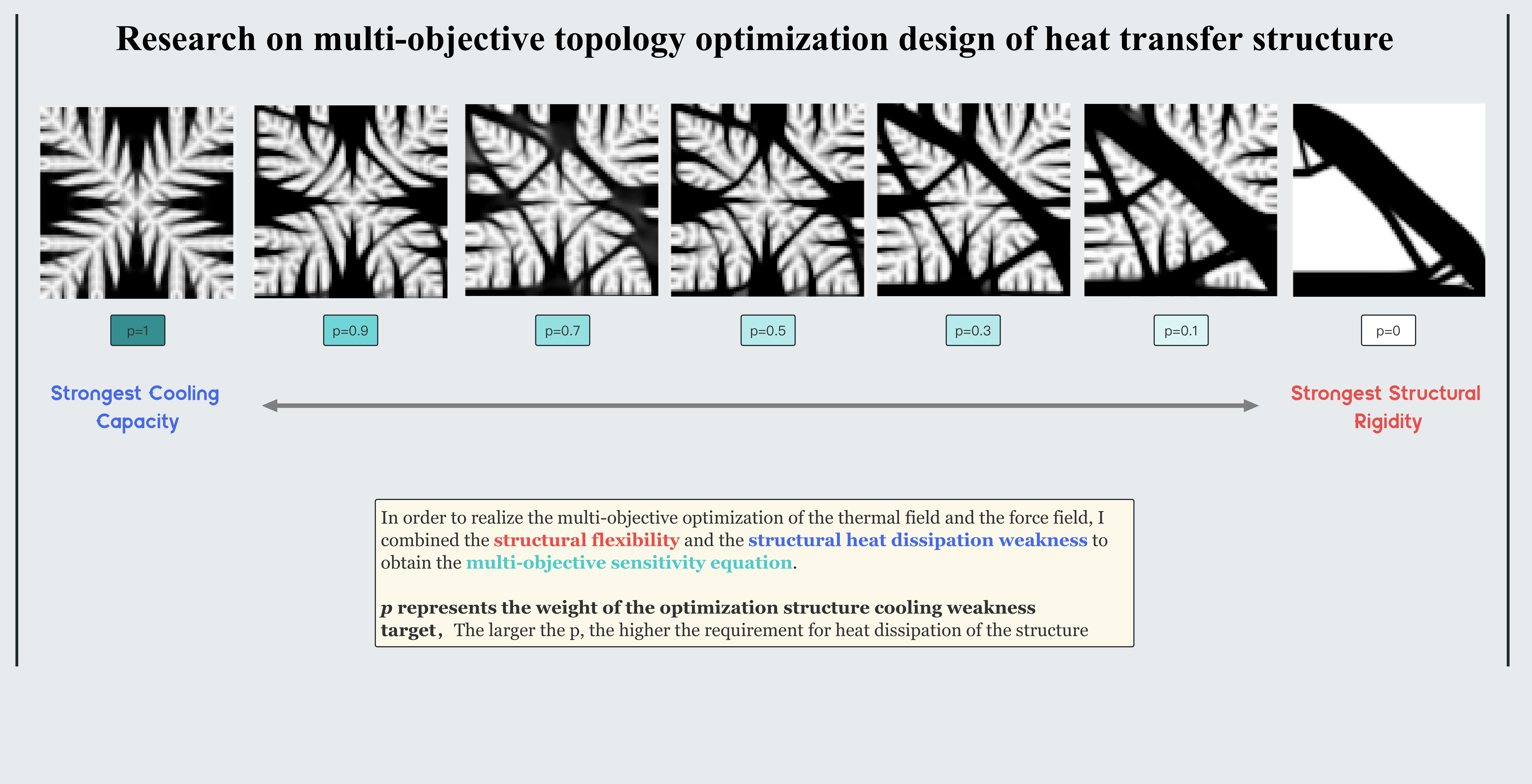