Course Project|Ergonomics
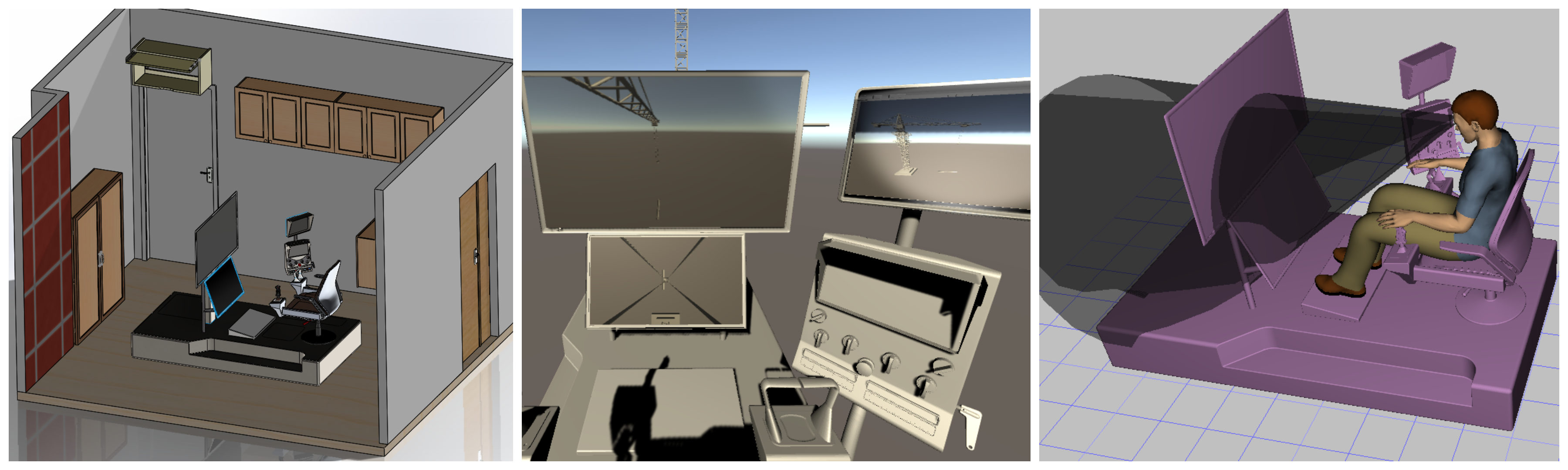
Introduction to ergonomics course projects. The operation requirements of tower cranes were analyzed, and a simple, efficient and safe remote tower crane operation mode was designed. Implement simulation with Unity.
Course Project Requirements
Design Background
The remote-controlled intelligent construction equipment represented by intelligent tower cranes and aerial building machines has innovatively subverted the traditional “worker-construction equipment-construction environment” operation mode, transforming workers to operate in real time at high altitude through remote control system, that is, “worker-remote control system-intelligent construction equipment-construction environment” operation mode.
As shown in the figure below, it includes the safety monitoring system (used to dynamically monitor the status of the tower crane in real time, anti-collision, remote warning, etc.) and the hook visualization system (used to guide the operation system of the operator, display the surrounding environment of the operation in real time, and assist the operator to correctly judge and operate). The picture comes from the Internet and is for reference only.
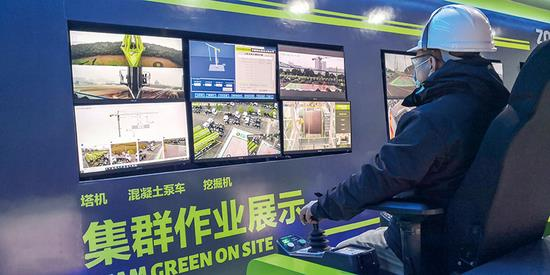
Schematic diagram of the remote control interface of the intelligent tower crane
Project Requirements
According to the functional requirements of the intelligent construction remote operating system, the interface of the intelligent tower crane remote control system is designed with people as a center, including but not limited to functional analysis and functional layout design:
-
VR simulation of the spatial relationship between the tower crane and the indoor control system;
-
Ergonomic simulation of seats and consoles of indoor control systems;
-
select the input device of the indoor control system;
-
Select the output equipment of the indoor control system;
-
Interactive interface design of indoor control system.
Specific Implementation Methods of The Project
-
Use tools such as Unity to carry out VR simulation of the spatial relationship between the tower crane and the console;
-
Use tools such as Jack to conduct ergonomics simulation of the chairs and workbenches in the workspace;
-
Use Axure and other prototype development tools to complete the interface design of the intelligent construction remote control system.
Design Inspiration
Tower cranes are divided into two categories: upper rotary tower cranes and lower rotary tower cranes. Among them, the bearing capacity of the former is higher than that of the latter, and in many construction sites we see is the up-swing type jacking tower crane with joint height. According to whether it can be moved, it is divided into: walking type and fixed type. The fixed tower crane tower body is fixed and does not rotate, installed on a whole concrete foundation, or installed on a strip or X-shaped concrete foundation, and the walking type can be divided into four types: crawler type, automobile type, tire type and track type. In the construction of houses, the fixed type is generally used. According to its luffing mode, it can be divided into two types: horizontal boom trolley luffing and boom luffing; According to its installation form, it can be divided into three types: self-elevating type, integral quick disassembly and assembly. The most widely used are down-swing, quick disassembly, rail-mounted tower cranes and jack-up tower cranes that can be used for four purposes (rail-mounted, fixed, attached and in-climbing). This project chose the most common up-swing tower crane in the construction site in life.
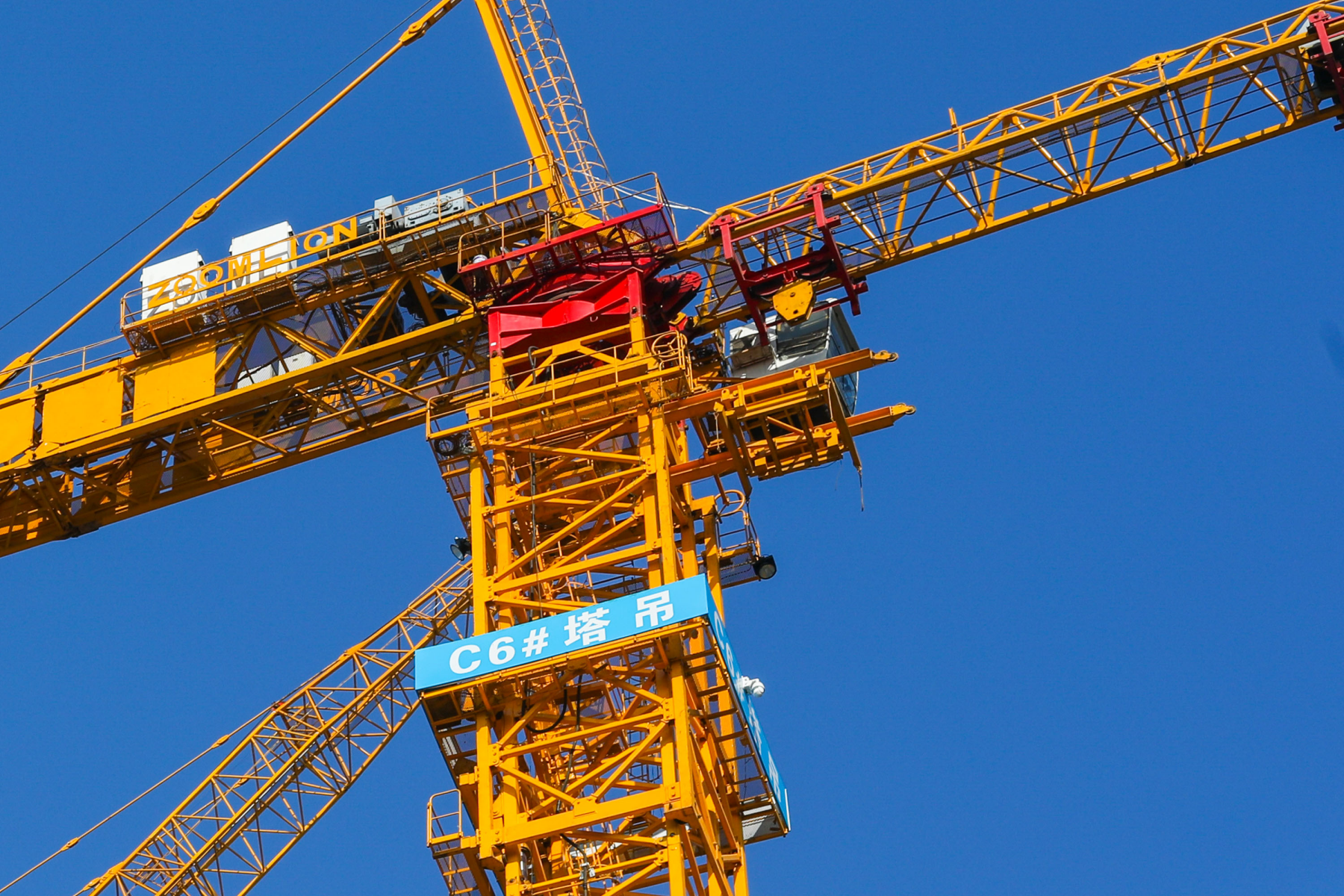
Tower crane
Tower crane control compartment inspiration: Cockpit in Japanese Mecha Anime: Mobile Suit Gundam SEED
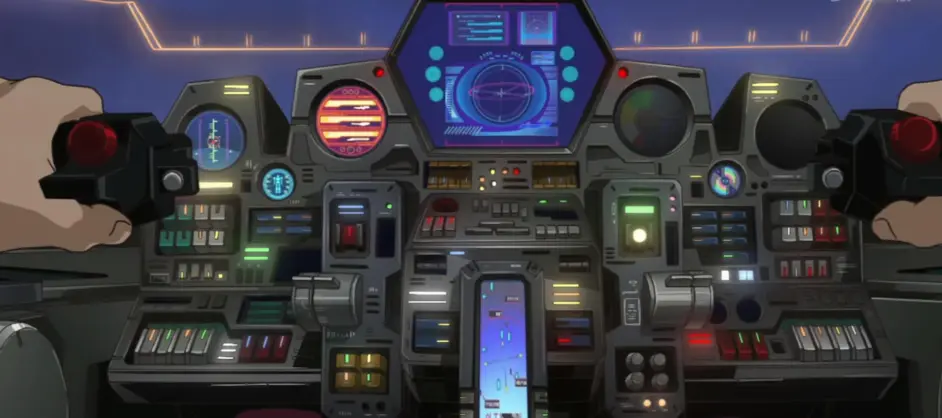
Picture of the cockpit panel shown in the anime
Design feature analysis:
- Comfortable and spacious seat, equipped with pedals, which is conducive to preventing the operator from fatigue of the spine, shoulders and neck caused by long-term driving.
- Multi-screen display system, around the operator’s head-up view. It can display video images of all sides of the large mecha, which is conducive to judgment and has high utilization of cockpit space.
- Multi-functional, integrated joystick. The operator does not need to leave the joystick when operating different functions.
- Highly integrated electronic instrument system for operators to quickly obtain the required data.
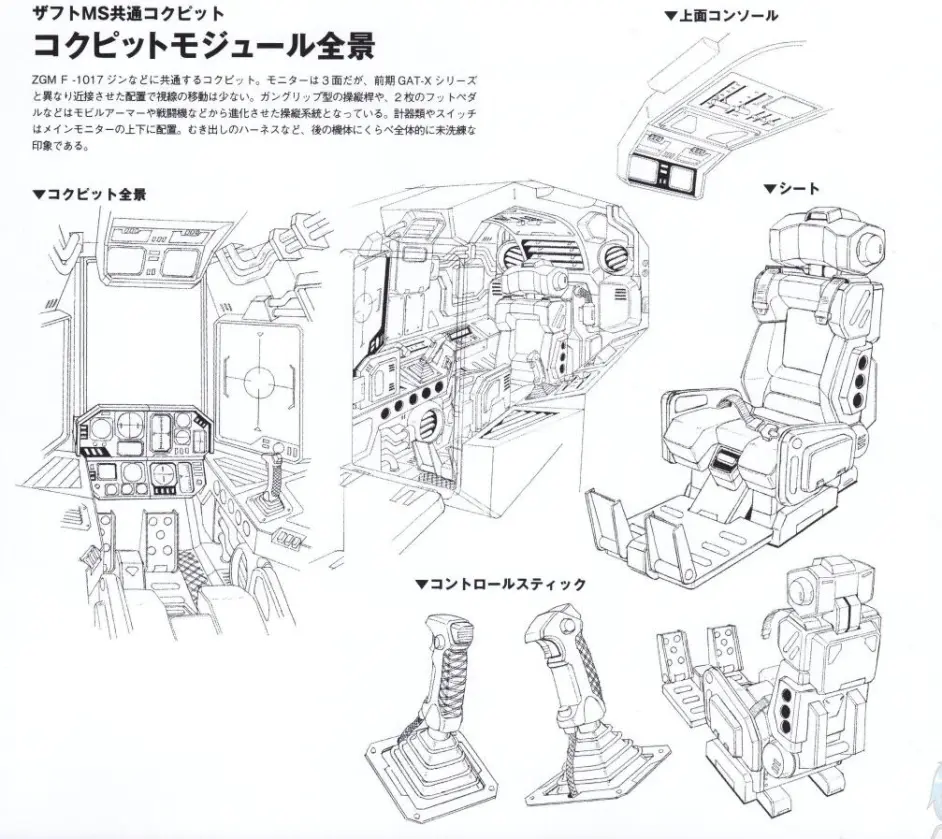
Design drawing of the cockpit
Joystick Design
I have completely designed a set of joysticks to help make it easier to operate the tower crane system.
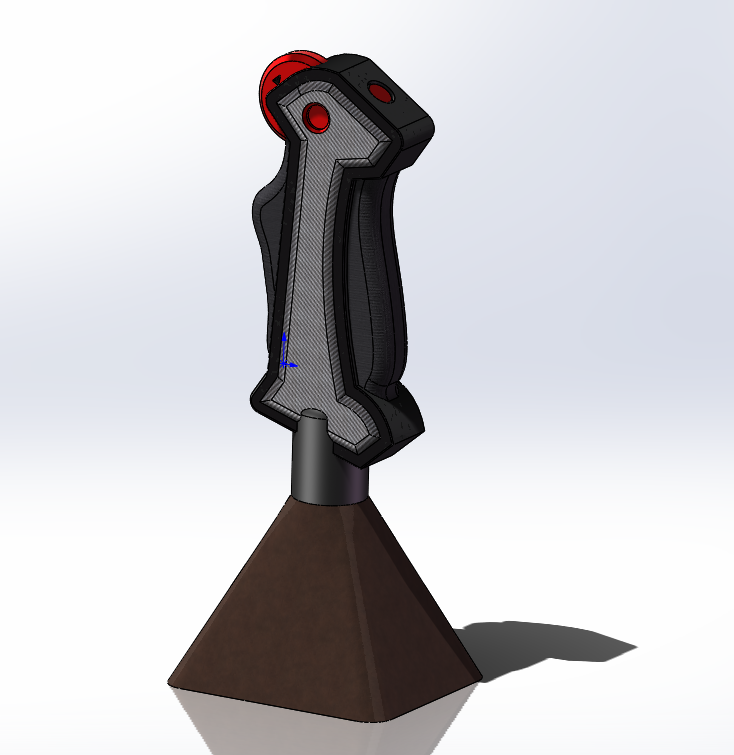
A 3D model of the joystick
Including trigger pitch, trigger roll and dial wheel three shafts, Corresponds to the three degrees of freedom of the tower crane.
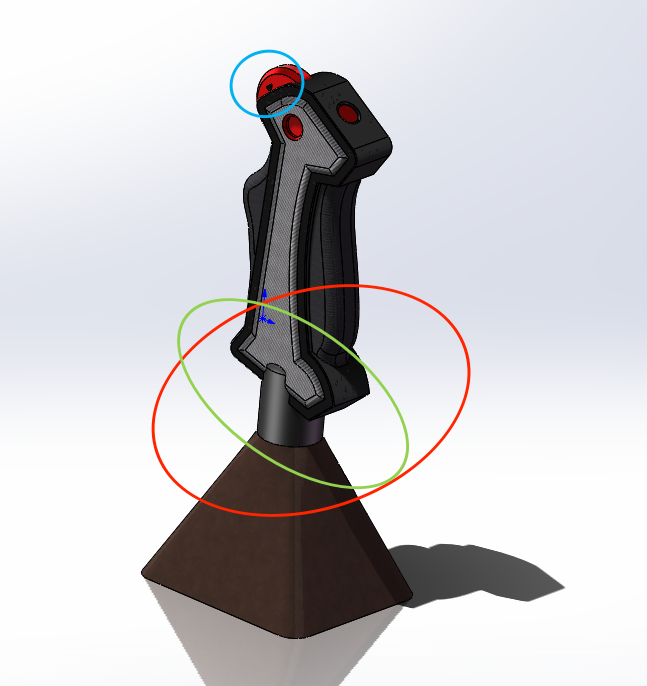
Joystick degree of freedom display
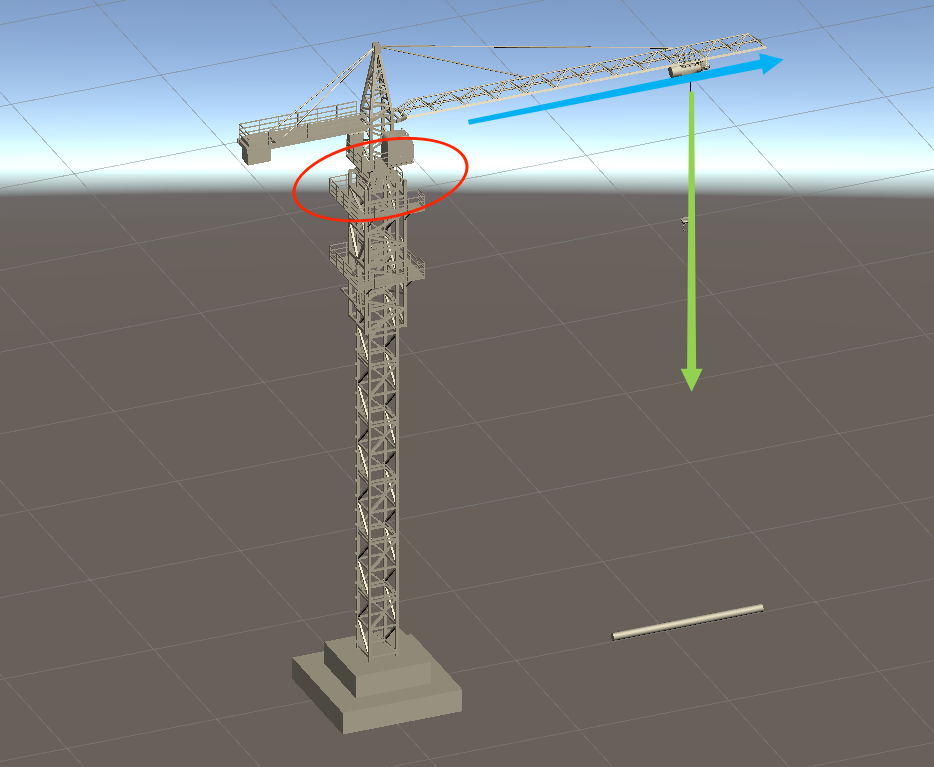
The joystick degrees of freedom correspond to the tower crane display
There is a tower crane emergency stop button on the top, which is recessed to prevent false touch.
Console Design
Multiple large displays are presented in front of the crane operator, and the position of the crane can be judged according to the information obtained from different perspectives. Helps operators complete tasks with concentration and efficiency.
Unity model of the console
Indoor console layout
Traditional Camera
Considering that crane operators may have traditional crane driving experience, the largest screen is used to show the traditional driving perspective. The camera uses a 100° wide-angle lens to simulate the human eye.
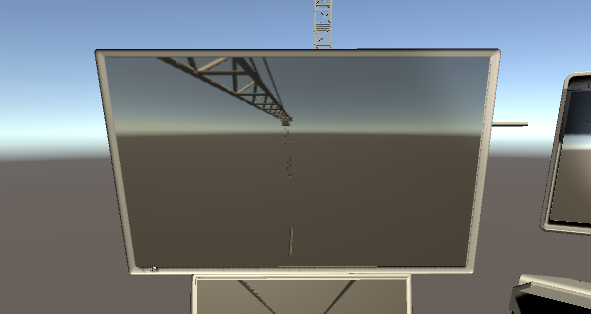
Operation screen of the Traditional Camera
Traditional Camera enables crane operators to quickly adapt to this driving style with experience.

Location diagram of the Traditional Camera
FPV Camera
Fpv Camera is installed at the tower crane trolley to transmit back the first-person view view. The screen set under the console is
Operation screen of the FPV Camera
FPV Camera enables crane operators to intuitively and precisely align loads.
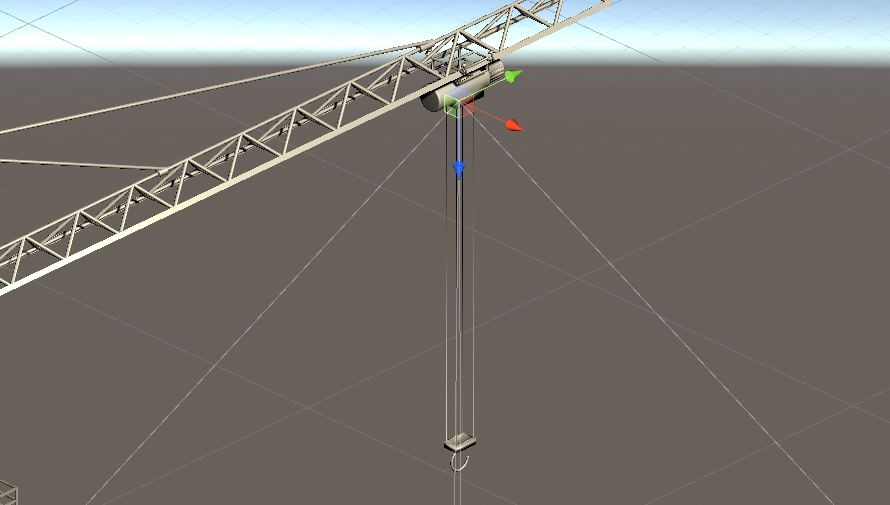
Location diagram of the FPV Camera
General Camera
General Camera can capture the entire picture of the tower crane, installed in adjacent high-rise buildings or aerial drones (mobile camera position can be controlled by keyboard)
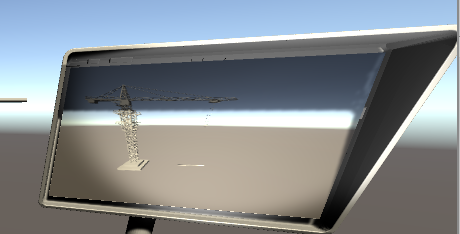
Operation screen of the General Camera
General Camera can avoid accidents caused by collisions between tower cranes and other obstacles, and can observe the overall situation of tower cranes. The frequency in use will be relatively low, so it is displayed on the right side of the console.
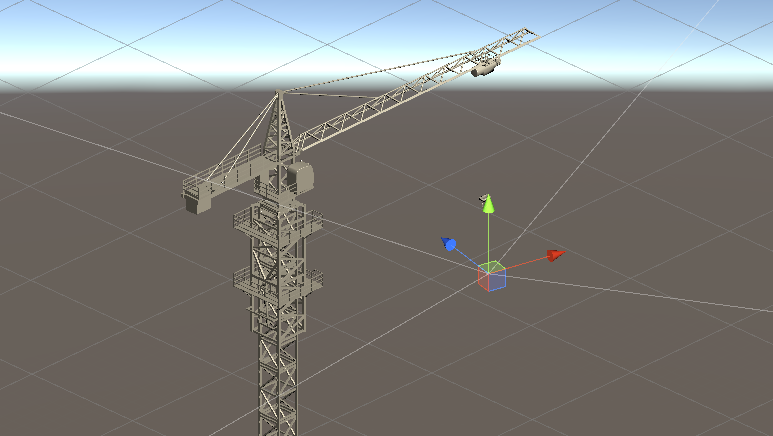
Location diagram of the General Camera
Unity Simulation
A method for Implementing a Screen to Display Camera Footage
Create cameras and render render camera images to render and output to Render
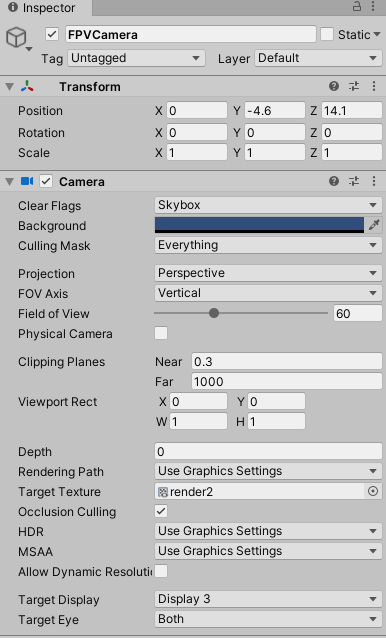

Create a plane in front of the display that is the same size as the screen, attach the render to its surface, and achieve the effect of displaying the live picture of the camera
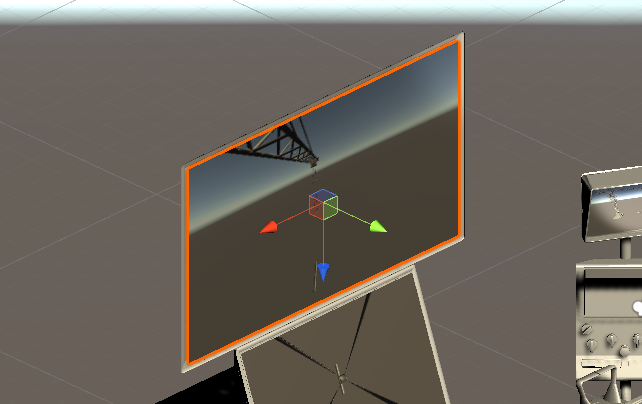
Preparation Before the Realization of the Motion
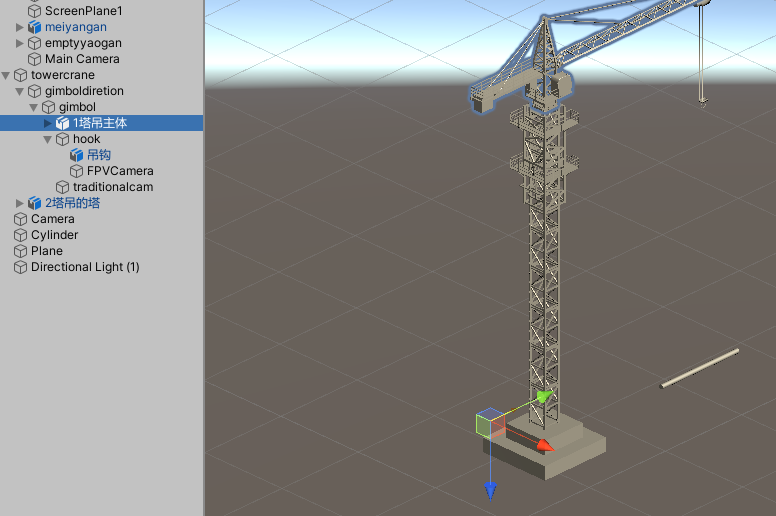
Using empty objects, changing the position of their center of gravity through a hierarchical relationship facilitates subsequent operations
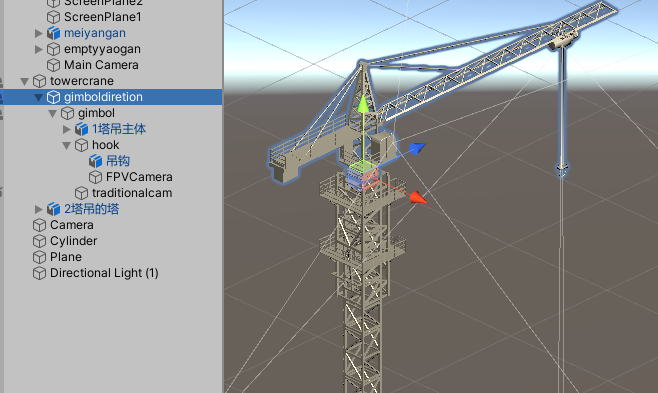
Implement Motion Control Using Unity C# Code
Hook Telescopic Control
Controls the scaling of the hook model in the y direction to achieve elongation and shortening
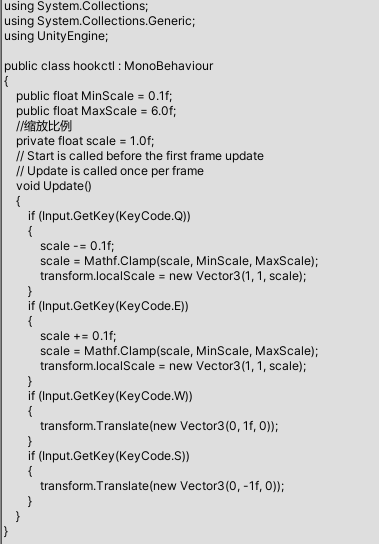
Hook Rotation Control
Taking the joystick as an example, the function is called to change its angle in all directions when the key is pressed. Note: Choose the object’s own coordinate system.
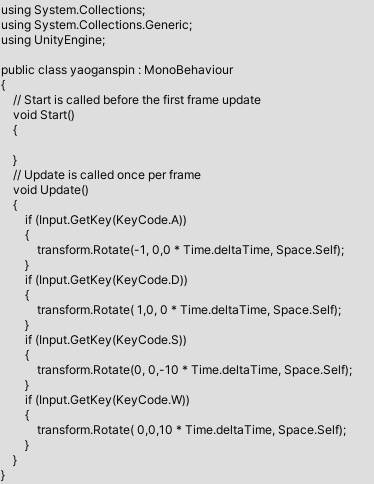
Hook Slide Control
In the case of a movable camera, a function is called when a key is pressed to give velocity to the object in all directions. Note: Choose the object’s own coordinate system.
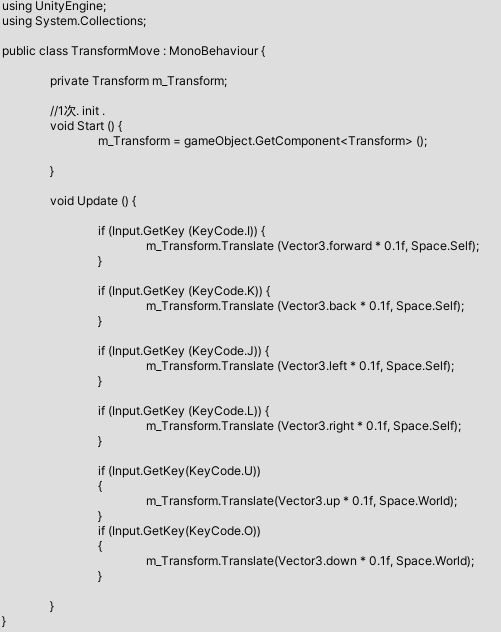
Unity Node Summary
Through this ergonomics project, the operation requirements of tower cranes were analyzed in depth, and a simple, efficient and safe remote tower crane operation mode was explored by using ergonomics knowledge. Through the new tool, Unity implemented simulation, and became familiar with Unity’s operation and development process.
Improvements Can Be Made:
The Unity simulation interface is not aesthetically pleasing, and there is no detailed study of how to add realistic materials, etc., so you should pay attention to it when using it in the future.
The telescopic hook is cleverly used to control the overall model telescopic, in fact, the tower crane trolley and the hook will be telescopic, and there is an obvious gang. After that, you can consider studying the use of rope modules to improve it.
There is no limit to the control of the joystick, and the joystick will rotate without limit. The joystick will be molded with the seat. The reason is that there is not enough understanding of C# to achieve the limitation of rotation angle.
Operating room scene simulation
Seat Design and Reference Standards
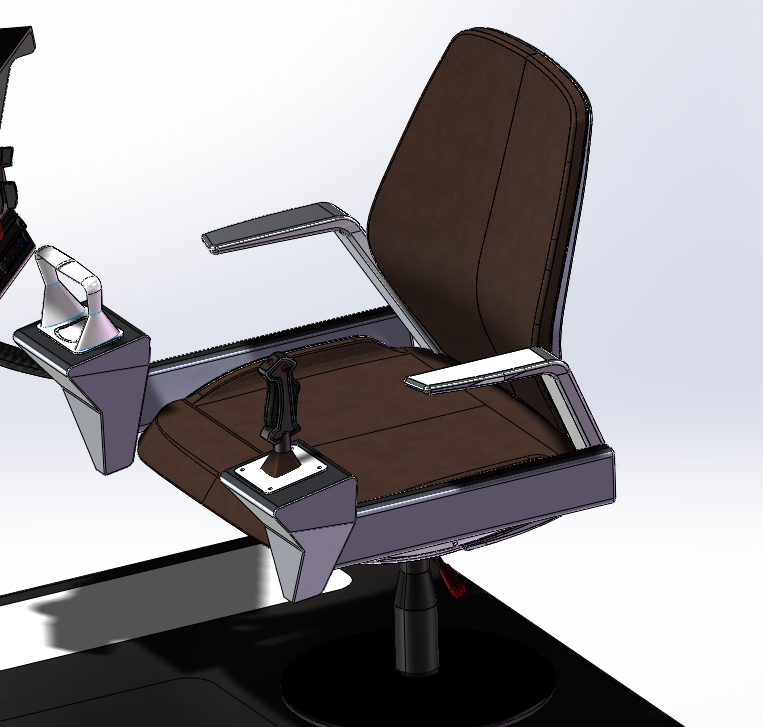
Seats designed for this project
Current Dimensional | Ergonomic Dimensional Requirements | |
---|---|---|
Seat Inclination | -4° | -4° |
Seat Depth | 300mm-500mm | 400mm-540mm |
Seat Width | 514mm | >430mm |
Effective Seat Back Width | 480mm | >360mm |
The seat designed this time basically meets the ergonomics requirements. In theory, it can provide a good user experience.
Operator Modeling
Given that tower crane operators are mostly males aged 20-45
Directly select the character model that comes with Siemens Tecnomatix Jack for simulation.
Jack's own male mannequin
Operator Visibility Analysis
The operator’s first-person view is shown in the figure
Operator's first-person view
Most of the field of view is the Traditional Camera screen Similar to traditional tower crane driving experience
Just bow your head slightly when you need to watch other screens
Conclusion: The design of the console makes the screen range that needs to be watched all within the visible field. Can easily obtain the required information.
Operator Accessibility Analysis
Through the analysis of the feasible region of the left and right hands, it can be seen that all the operating components, joysticks, buttons, etc. of the console are all within the maximum comfort range of the operator’s body. The operator can comfortably operate all functions with minimal changes in the body’s center of gravity.
Axure Operation Interface Design
Design Requirements
The tower crane operating system designed this time has a variety of usage scenarios.
- Remote control: When the operator is not on the job but has urgent tasks to deal with, he can open the remote operating system and quickly operate the tower crane to complete the task.
- Supervision and inspection: The site management personnel can open the operating system to check the working status of the operator, and can directly assign tasks.
- Manipulation teaching: For beginners of tower cranes, master craftsmen can use this system to guide beginners to learn manipulation skills, while ensuring the safety of the construction site.
Interface Video Display
Start Interface
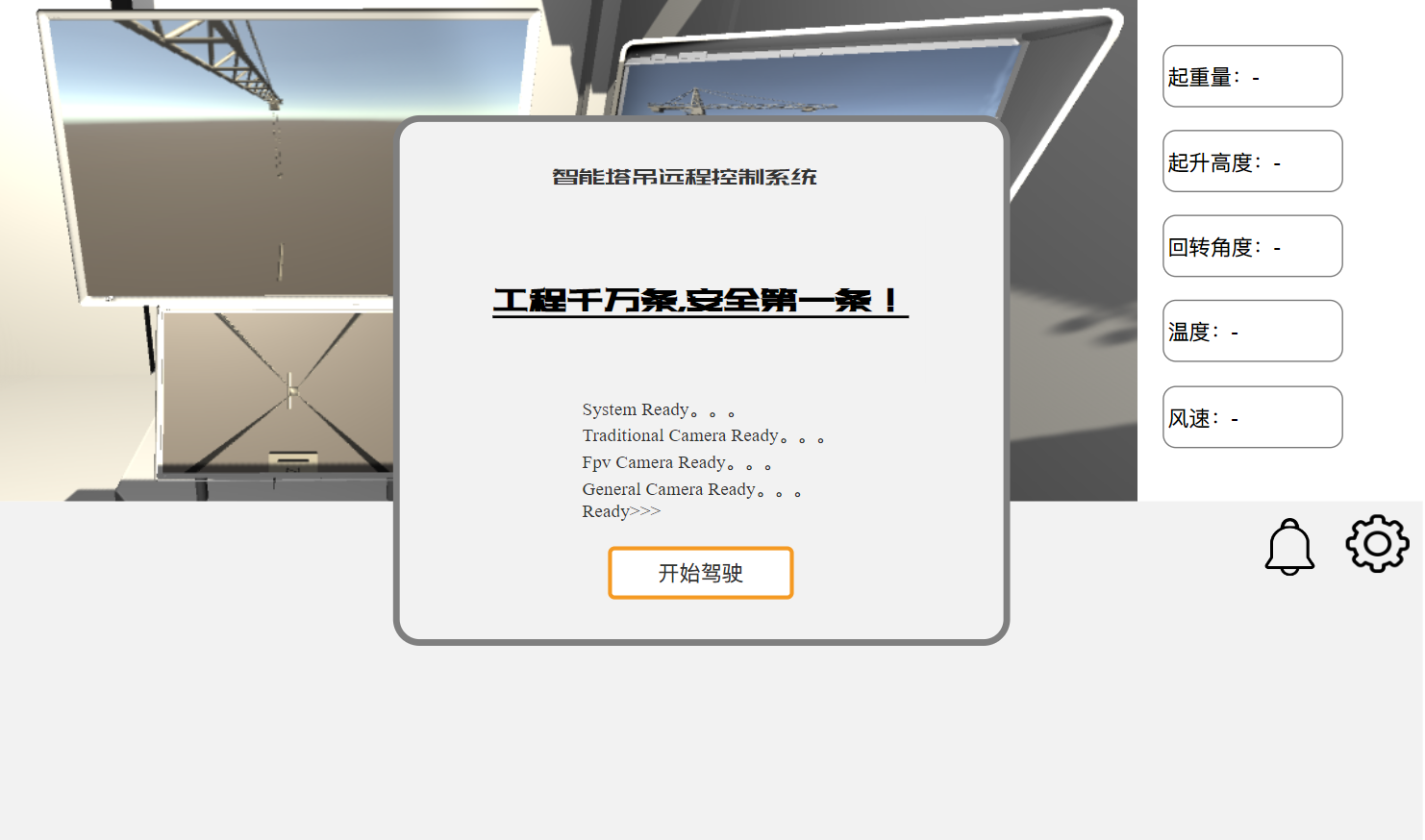
Start Interface
-
Remind the operator to pay attention to safety.
-
Display system and camera self-test information.
-
Click “Start Driving” to enter the main interface
Main Interface
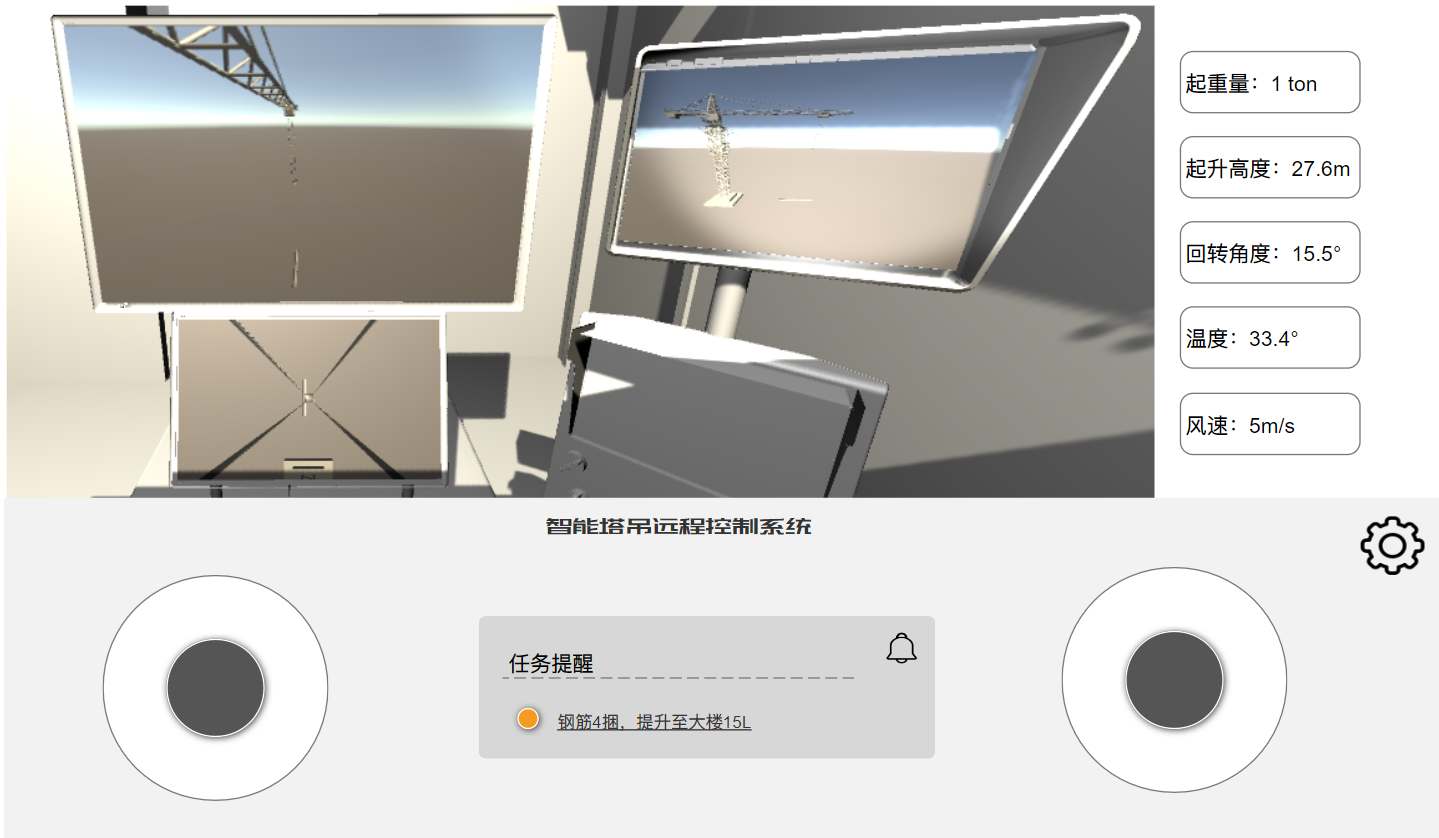
Main Interface
-
The picture is a real-time picture simulating the real driving experience
-
The right side of the screen will display the tower crane status and environmental parameters
-
Below are two joysticks, which correspond to the movement of the tower crane.
-
The task reminder bar between the two joysticks will display the current task.
Task Reminder Interface
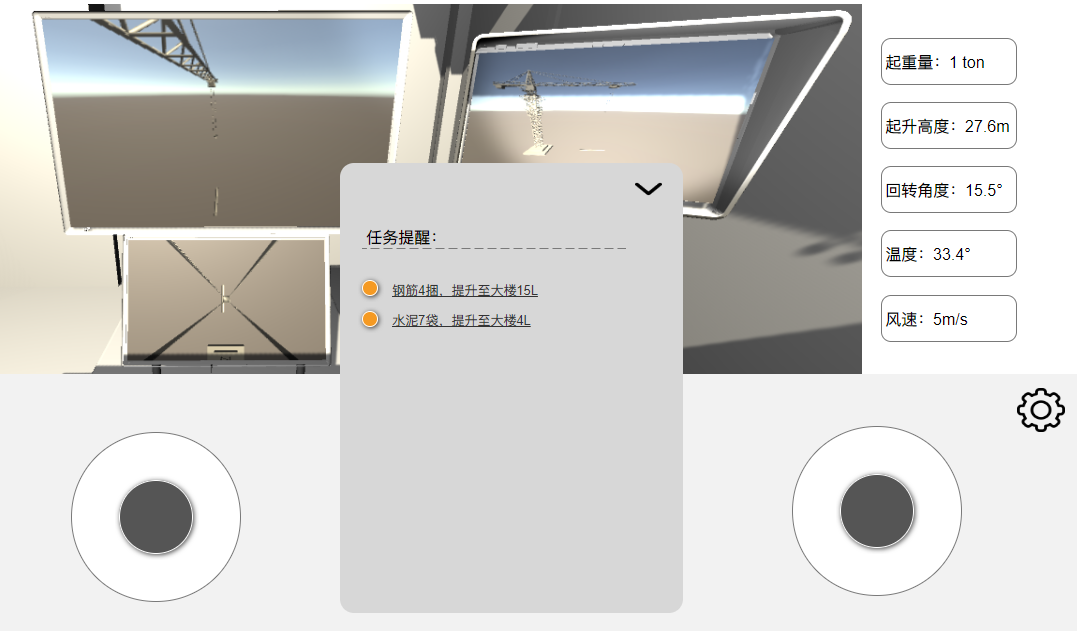
Task Reminder Interface
-
Click on the task reminder to call out the task menu
-
Operators can quickly view all tasks
System Settings
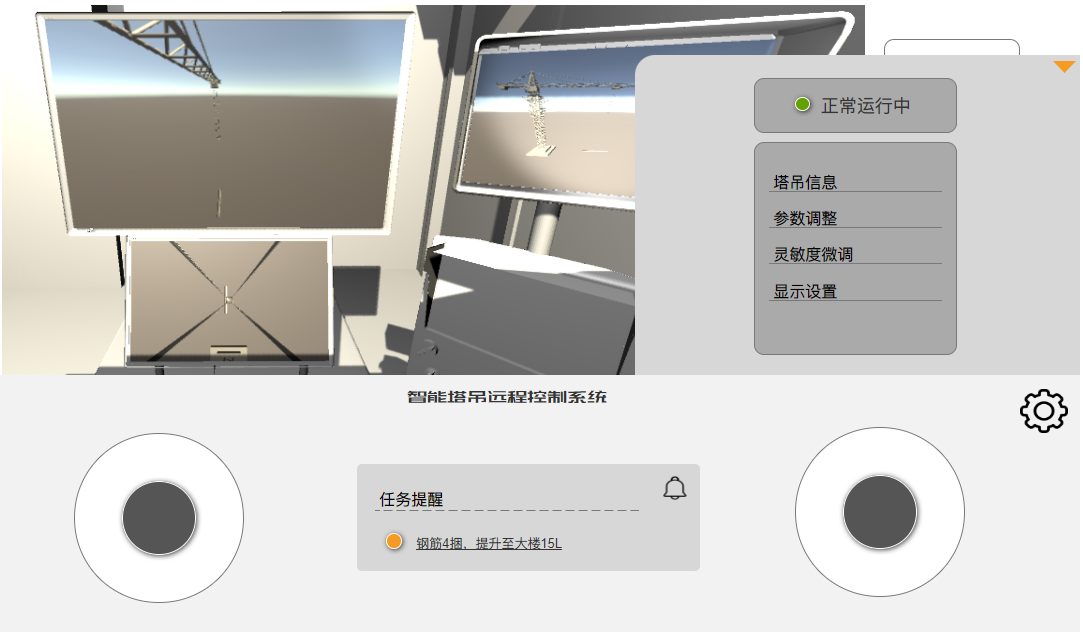
System Settings
-
Click the gear button to call out the system settings
-
The operator can view the running status of the tower crane, check the tower crane information, adjust parameters, fine-tune sensitivity and adjust the display.